In the world of industrial machinery, coil upenders stand as vital components in the seamless movement of massive coil materials, often weighing tons. They're machines that skillfully rotate coils, allowing for efficient handling in manufacturing environments. Steel industries and sheet metal fabricators rely heavily on these machines to improve operational workflows. The coil upender's function may seem straightforward at first glance, but the pricing intricacy that surrounds it is anything but simple.
Coil upenders, despite their elementary operational purpose, are influenced by a plethora of cost determinants. Factors like the machine's capacity, the materials used in its construction, and the technology embedded within it, all play a critical role in shaping its pricing. For instance, a basic upender with manual features differs vastly in cost from its automated, high-capacity counterpart. This variance is often dictated by production efficiency demands and the specific needs of an industry, revealing a complex interplay of technological and economic variables.
What drives the cost disparities in coil upender pricing? The answer lies in understanding both the subtle and overt elements that govern these machines' manufacture and operation. As we delve deeper, we will uncover the strategic choices that lead companies to invest significantly in such indispensable equipment.
**Claim:** Understanding the factors influencing coil upender prices is paramount for industries aiming to optimize their budget allocations and operational efficiencies.
How Does Capacity Affect Coil Upender Costs?
The capacity of a coil upender, defined by the weight it can handle, is a primary determinant of its cost. In an industrial setting, upenders must be capable of managing various coil sizes and weights, which range from manageable to staggering. For instance, an upender designed to maneuver a 10-ton coil is built differently compared to one servicing a 50-ton coil.
Consider the reinforced structures and robust engines required for higher capacity upenders, which naturally lead to increased manufacturing costs. High-strength materials like alloy steels are often utilized to ensure durability and safety when handling heavier weights. This requirement impacts the overall production expenditure, thus pushing the final price point higher.
Moreover, the technology integrated within high-capacity upenders is often advanced, offering automated control options, precision handling, and safety features. Such systems reduce human intervention and align operations with modern efficiency standards. The cost implication here is significant, as industries might find these technologies essential for streamlined processes, despite the higher initial expenditure.
Interestingly, the decision to invest in a high-capacity coil upender can be a strategic one, aiming to future-proof operations against potential increases in production scale or coil weight. This foresight can lead to more substantial upfront investments, but with long-term operational savings and increased productivity as essential returns.
A scenario where an automotive manufacturer anticipates an upsurge in production pipeline might opt for a high-capacity upender. This choice, while initially costlier, ensures that the equipment aligns with forthcoming demand, potentially saving millions in operational changes down the line.

What Role Does Technology Play in Pricing?
| Upender Type | Technology Level | Price Range ($) |
|--------------|------------------|----------------|
| Manual | Basic | 5,000 - 10,000 |
| Semi-Automatic| Intermediate | 10,000 - 20,000|
| Fully Automatic | Advanced | 20,000 - 50,000|
| IoT-Enabled | Cutting Edge | 50,000 - 75,000|
| AI-Integrated| State-of-the-art | 75,000+ |
The integration of technology in coil upenders significantly influences their prices. As shown in the table, manual machines, offering only the most basic functionality, stand at the lower end of the price spectrum. These machines require more operator intervention, which can be a cost-effective choice for small-scale operations.
As we transition to semi-automatic and fully automatic systems, a marked increase in cost is evident. These machines often feature advanced programmable logic controls (PLC), allowing for more precise operations and reduced human error. Industries engaging in high-volume production often prefer these models due to their efficiency in handling repetitive tasks.
Cutting-edge innovations such as Internet of Things (IoT) capability and AI integration further escalate the price. These systems allow for predictive maintenance, better machine uptime, and enhanced data analytics, aiding decision-making and reducing long-term operational costs. For instance, a large steel production company might find value in investing in AI-integrated coil upenders to optimize their production lines, despite the steep initial cost.
Thus, technology plays a pivotal role in not just the price of coil upenders but also in enhancing operational efficiency and future scalability. The selection often depends on a company's immediate needs versus its strategic long-term goals.
How Do Material Choices Impact Costs?
Material selection in coil upender construction is another fundamental cost driver. The specific materials used determine both the durability and the safety of the machine, which in turn affect its pricing. High-strength steels and alloys are commonly preferred for their ability to withstand significant mechanical stress and wear over extended periods.
For instance, an upender made from low-carbon steel might suffice for lighter applications but would wear out faster when used beyond its intended capacity. This is where higher-quality materials come into play—while they increase the initial manufacturing cost, they promise longevity and consistent performance under demanding conditions.
The coatings applied to these materials also add to the cost. Protective finishes, such as corrosion-resistant coatings, are essential for machines exposed to harsh environments. This becomes an added expense but ensures the machine remains operational for a longer time without costly repairs or replacements.
Furthermore, the sustainability of materials has emerged as an influencing factor. Industries are increasingly conscious of their environmental impact, leading some to opt for eco-friendly material choices. These might cost more upfront but yield returns in the form of a smaller environmental footprint, which can be a strategic advantage in today's eco-conscious market.
Ultimately, the choice of materials reflects a balance between cost, durability, and environmental considerations, heavily influencing the pricing of coil upenders.
Are Off-the-Shelf or Custom Solutions More Cost-Effective?
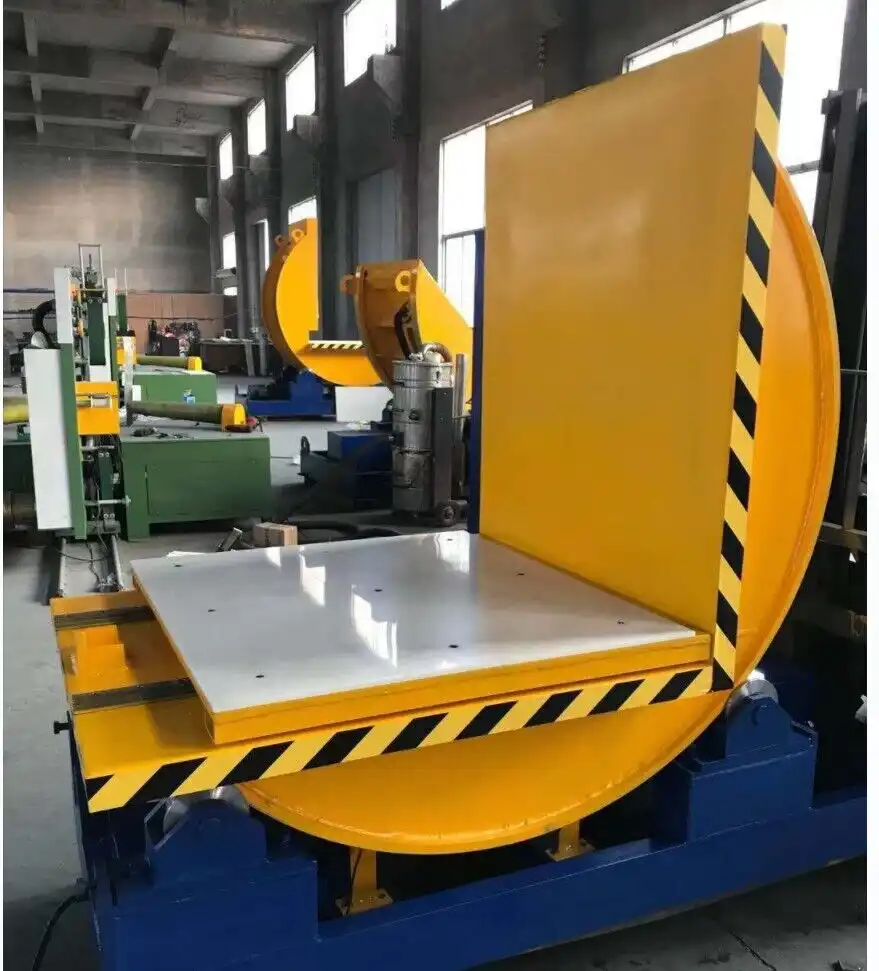
| Solution Type | Customization Level | Estimated Cost ($) |
|---------------------|---------------------|--------------------|
| Off-the-Shelf | Minimal | 5,000 - 15,000 |
| Basic Customization | Moderate | 15,000 - 30,000 |
| Extensive Customization| High | 30,000 - 60,000 |
| Fully Custom | Tailored | 60,000+ |
| Modular Systems | Adaptable | 20,000 - 50,000 |
Choosing between off-the-shelf and custom coil upenders presents another layer of pricing complexity. Off-the-shelf solutions typically carry a lower price tag due to economies of scale in production. These options are suitable for businesses with standard operations and less specific needs.
However, industries often encounter unique operational challenges that necessitate custom solutions. This involves tailoring the upender's design, technology, and capacity to meet specific demands—resulting in higher costs due to specialized engineering and manufacturing processes.
The table illustrates the price gradient from basic to extensively customized solutions. While custom solutions typically start at higher prices, they offer operational advantages like enhanced performance, reduced downtime, and alignment with precise production processes. For instance, a specialized manufacturing firm might invest in a fully custom coil upender to meet stringent safety standards or to achieve a specific production speed.
Modular systems present a middle ground, offering adaptability and incremental upgrades, catering to evolving needs without a full custom overhaul. This approach can be more cost-effective in the medium term, especially for industries expecting gradual growth or change.
Ultimately, the decision hinges on current operational needs versus potential future demands, impacting the cost-effectiveness of each choice.
What's a Common Misconception vs. Reality About Pricing?
One common misconception is that newer technology or higher capacity automatically translates to the best value. While it's true that cutting-edge technology and high-capacity machines offer numerous benefits, these attributes alone do not guarantee optimal value for every business.
**True Fact:** Advanced technology often improves operational efficiency, leading to long-term savings.
This is evident in many high-capacity upender models where automation reduces labor costs, and IoT integration enhances predictive maintenance, minimizing downtime. Companies focusing on high-volume production can benefit immensely from these advancements.
**False Fact:** Every business needs the most advanced and high-capacity coil upender.
In reality, smaller operations or those with specific niche requirements might find more value in manual or semi-automatic options. These machines, though less technologically advanced, meet their needs without unnecessary expense. Thus, understanding the specific demands of one's operation is crucial to making a cost-effective purchasing decision.
What is the Impact of Industry-Specific Needs?
Different industries, from automotive to construction, have varying requirements for coil upenders, each influencing pricing structures. For instance, the automotive industry might prioritize precision and speed to enhance production lines, whereas construction sectors focus on durability and robustness to handle rugged conditions.
In automotive manufacturing, coil upenders must integrate seamlessly with robotic systems for rapid handling and positioning. This requirement demands advanced automation and synchronization capabilities. The cost of these machines reflects the need for precision engineering and technology integration, often resulting in higher expenditure but yielding faster production cycles and reduced labor costs.
Conversely, construction industries often operate in less controlled environments, necessitating machines that can withstand extreme conditions. Here, the priority might shift towards rugged construction and ease of maintenance, potentially leading to different material and design choices that influence cost.
Industries with specific safety regulations also drive upender pricing. Compliance with these standards requires additional safety features, quality certifications, and often custom-design elements, contributing to increased costs but ensuring legal adherence and worker safety.
Industry needs, therefore, not only dictate the features and technology integrated into coil upenders but also their pricing, reflecting a delicate balance between performance, compliance, and cost.

How Can Numerical Data Guide the Purchasing Decision?
| Industry | Cost Range ($) | Average Lifespan (Years) |
|-----------------|----------------|--------------------------|
| Automotive | 30,000 - 80,000| 10-15 |
| Construction | 25,000 - 70,000| 8-12 |
| Manufacturing | 20,000 - 60,000| 10-14 |
| Steel Production| 35,000 - 100,000| 12-18 |
| Logistics | 25,000 - 65,000| 8-12 |
Numerical data serves as a critical tool in guiding the purchasing decision of coil upenders. As illustrated in the table, different industries exhibit variability in cost ranges and average machine lifespans. These figures provide benchmarks that businesses can use to assess whether their investment aligns with industry standards.
The cost range and lifespan data help companies evaluate the return on investment (ROI) for potential purchases. A high initial cost might be justified by a longer lifespan and lower maintenance needs, ensuring that the upender remains functional and cost-effective throughout its operational life.
Moreover, numerical insights can highlight discrepancies between current spending practices and industry averages. For instance, an automotive business experiencing unusually rapid turnover of coil upenders may discover through data analysis that their maintenance practices or operating conditions are influencing machine longevity, thereby adjusting their selection criteria accordingly.
Ultimately, employing numerical data helps businesses make informed decisions, ensuring their coil upender investment supports their operational goals and delivers maximum value over time.
What Are the Key Takeaways and Advice for Potential Buyers?
When purchasing a coil upender, understanding the various factors influencing its price is crucial. Here's some actionable advice for potential buyers:
1. **Assess Capacity Needs:** Evaluate your current and future production scale to choose an upender with appropriate capacity. Over- or under-estimating can lead to unnecessary costs or operational inefficiencies.
2. **Consider Technological Integration:** While advanced technology offers numerous benefits, it's essential to balance these against your actual operational needs and budget constraints. Prioritize technology that delivers tangible operational benefits.
3. **Evaluate Material and Durability:** Invest in machines made from durable materials with necessary protective coatings, especially if operating in harsh environments.
4. **Analyze Custom vs. Off-the-Shelf Options:** Weigh the benefits of customization against your specific operational needs. Custom solutions may offer enhanced performance but come at a higher cost.
5. **Use Industry Data for Benchmarking:** Employ numerical data to guide your decision-making, ensuring your investment aligns with industry average costs and lifespans.
**Conclusion:** Coil upender pricing is a multifaceted subject intertwined with capacity, technology, material choice, and industry-specific demands. By understanding these elements, businesses can make informed purchasing decisions that optimize their investments and enhance operational efficiency. **Claim:** Insightful analysis of coil upender cost influences equips businesses to better allocate resources, ensuring they secure machinery that supports both current operations and future growth.
More machines for the: coil upenders